Description
As a market leader, We likely have a significant presence and expertise in the installation of CNC machines. This involves setting up the machines, configuring their parameters, and ensuring they are fully operational. Proper installation is crucial to optimize the performance and reliability of CNC machines.
Being a market leader comes with responsibilities and opportunities. It’s important to stay up-to-date with the latest advancements in CNC technology and continually adapt your offerings to meet the evolving needs of your customers. Additionally, maintaining strong customer relationships, delivering exceptional service, and keeping a pulse on industry trends will help solidify your position as the market leader in CNC machine installation and training.
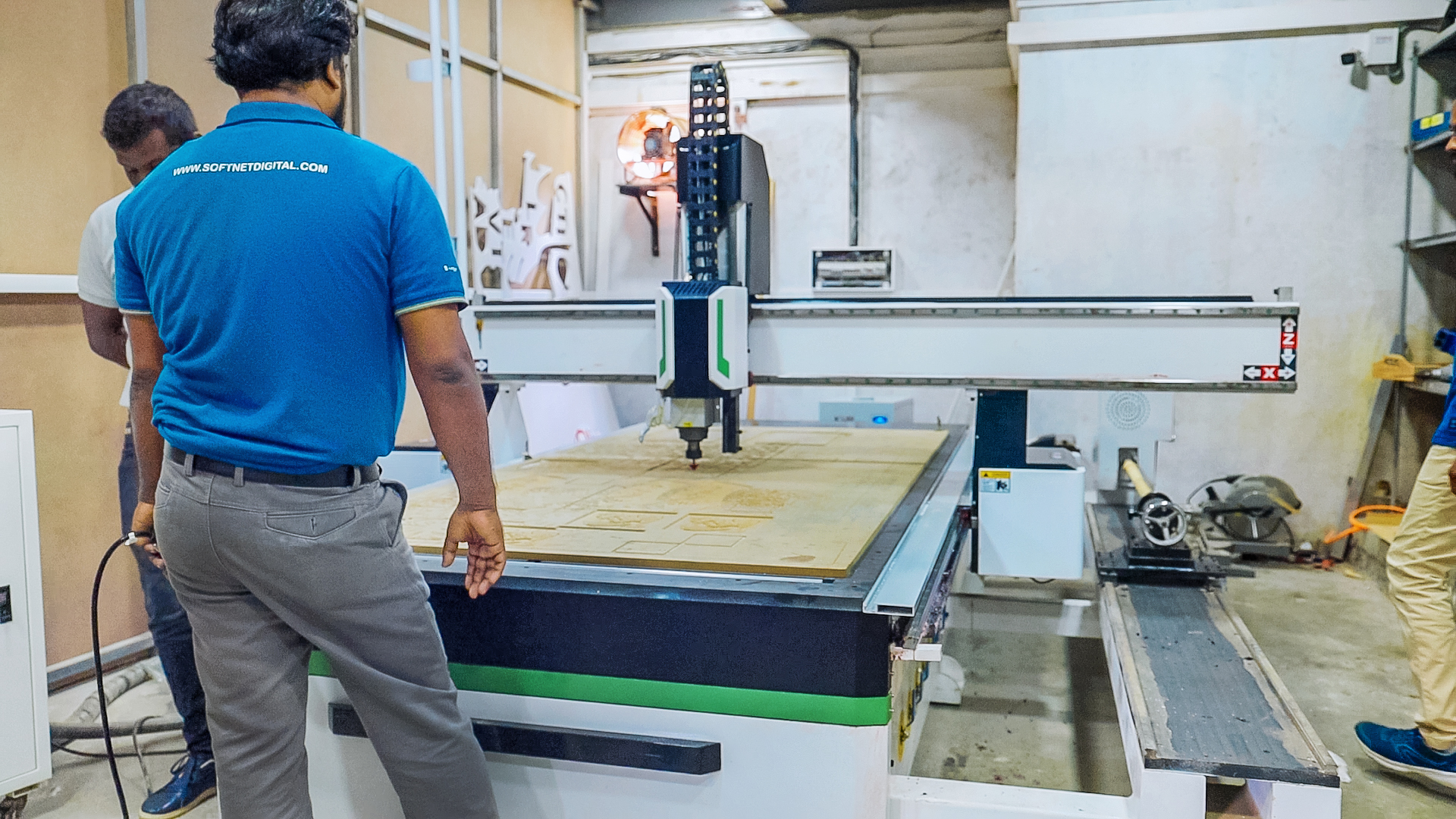
- Accuracy and Precision: CNC machines are known for their ability to produce highly accurate and precise components. However, to achieve optimal performance, proper installation is essential. Precision alignment of machine components, calibration of sensors, and accurate programming are critical during installation. A well-installed CNC machine ensures that it operates with the intended precision, leading to high-quality finished products.
- Machine Performance and Reliability: Correct installation of CNC machines helps optimize their performance and ensures reliable operation. This involves setting up mechanical components, such as spindles and linear guides, and configuring electrical systems, such as motor drives and controllers. By following manufacturer guidelines and best practices, potential issues and errors can be minimized, leading to smoother operation and reduced downtime.
- Safety: CNC machines can be powerful and complex, involving moving parts, high-speed cutting tools, and automated processes. Proper installation helps ensure that safety features and precautions are implemented correctly. It includes safety interlocks, emergency stop mechanisms, and machine guarding. By prioritizing safety during installation, you create a safer working environment for operators and reduce the risk of accidents.
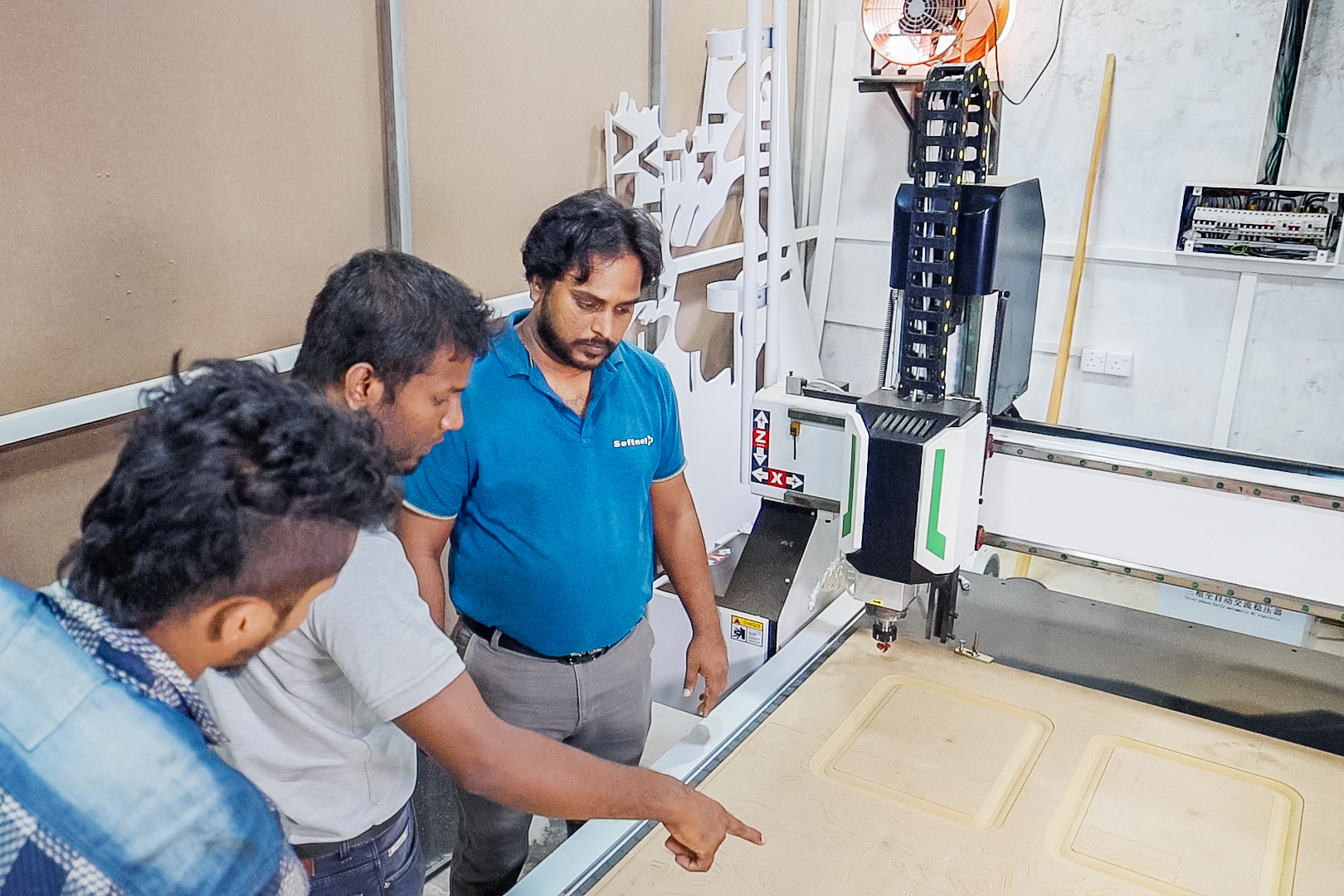
- Optimal Tooling and Workholding: CNC machines require suitable tooling and workholding fixtures to perform efficiently. During installation, consideration should be given to selecting the right tools, tool holders, cutting parameters, and workholding solutions. Proper training can help operators understand the nuances of tool selection, workpiece setup, and fixture alignment, enabling them to maximize the machine’s capabilities and productivity.
- Knowledge Transfer: CNC machine training provides operators and technicians with the necessary knowledge and skills to operate, program, and maintain the machines effectively. Training programs cover topics such as machine controls, programming languages (e.g., G-code), tool offsetting, troubleshooting, and preventive maintenance. By investing in comprehensive training, you empower your staff to utilize the CNC machines optimally, improve productivity, and minimize errors.
- Adaptability and Continuous Improvement: CNC technology continues to evolve rapidly. Regular training sessions allow operators and technicians to stay updated with the latest advancements in CNC systems, software, and machining techniques. This adaptability ensures that your workforce remains competent and capable of leveraging new features and capabilities to improve processes and product quality.
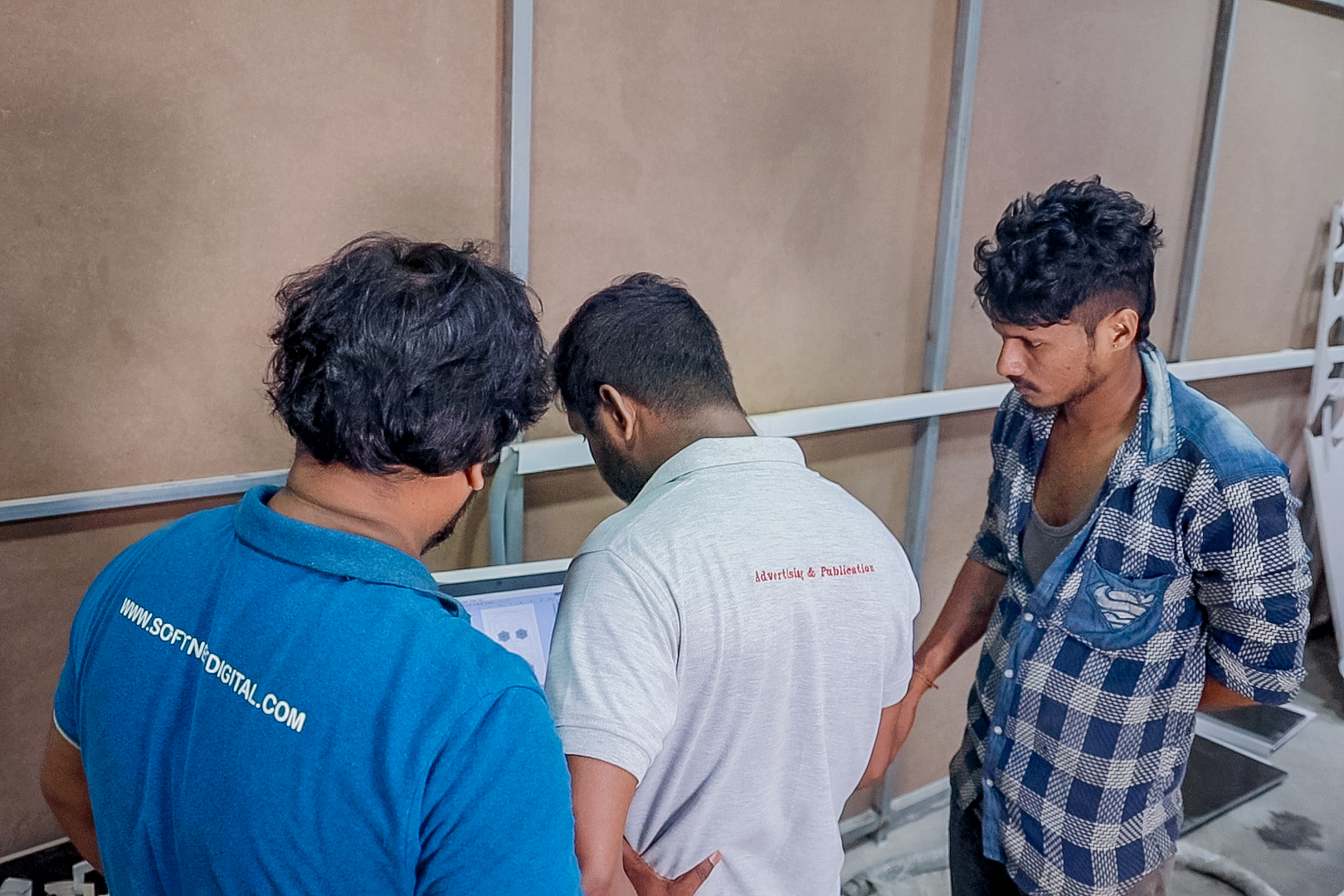
CNC machine installation and training are vital for achieving accurate and precise machining, optimizing performance and reliability, ensuring safety, maximizing productivity, and staying up-to-date with evolving technology. By prioritizing these aspects, you can enhance your competitiveness in the market and deliver exceptional results to your customers.
Reviews
There are no reviews yet.